Six Sigma: SPC And TQM In Manufacturing And Services

In today's competitive global market, organizations in both manufacturing and service industries are faced with relentless pressure to deliver high-quality products and services at an affordable price. Meeting this challenge requires a commitment to quality control and continuous improvement, two fundamental principles embodied by statistical process control (SPC) and total quality management (TQM).
Statistical Process Control (SPC)
SPC is a data-driven approach to quality control that enables organizations to identify and eliminate sources of variation in their processes. It involves collecting and analyzing data from key process parameters to determine whether they are within acceptable limits. If any parameters fall outside these limits, engineers and quality inspectors can investigate the process and take corrective action to bring it back under control.
5 out of 5
Language | : | English |
File size | : | 5561 KB |
Text-to-Speech | : | Enabled |
Screen Reader | : | Supported |
Enhanced typesetting | : | Enabled |
Word Wise | : | Enabled |
Print length | : | 154 pages |
Key Elements of SPC:
- Sampling: Drawing a representative sample of products or data from the process at regular intervals.
- Data collection: Recording key process parameters, such as dimensions, weights, or service times.
- Statistical analysis: Using statistical techniques to determine if the data falls within specified limits.
- Process monitoring: Continuously monitoring the process to identify trends or changes that may indicate a shift in quality.
Benefits of SPC:
- Reduces process variation and improves product quality
- Identifies sources of defects and errors early in the process
- Provides data-driven evidence to support process improvements
- Helps establish and maintain customer confidence
- Minimizes waste and rework costs
Total Quality Management (TQM)
TQM is a holistic approach to quality management that extends SPC beyond the production floor to all aspects of an organization's operations. It involves empowering employees, encouraging customer feedback, and creating a culture of continuous improvement. The ultimate goal of TQM is to meet or exceed customer expectations consistently.
Key Elements of TQM:
- Customer focus: Prioritizing customer satisfaction and understanding their needs.
- Employee involvement: Empowering employees to identify and solve problems.
- Continuous improvement: Establishing a culture where all employees are constantly looking for ways to improve processes.
- Data-driven decision-making: Using data to inform quality improvement initiatives.
- Process management: Optimizing processes to reduce waste and improve efficiency.
Benefits of TQM:
- Enhances customer satisfaction and loyalty
- Reduces costs and improves profitability
- Increases employee morale and productivity
- Fosters a culture of innovation and continuous learning
- Strengthens the organization's competitive advantage
Integration of SPC and TQM
SPC and TQM are complementary approaches that can be integrated to create a comprehensive quality management system. SPC provides the data-driven foundation for process control, while TQM provides the framework for continuous improvement and customer focus.
Implementation of SPC and TQM in Manufacturing
In manufacturing, SPC and TQM can be effectively implemented to:
- Reduce manufacturing defects and improve product quality
- Optimize production processes to minimize waste and downtime
- Track key performance indicators (KPIs) and identify areas for improvement
- Create a culture of continuous improvement among operators and engineers
- Foster collaboration between production and quality assurance departments
Implementation of SPC and TQM in Services
In service industries, SPC and TQM can be used to:
- Monitor and improve service standards, such as response times and customer satisfaction levels
- Identify and address customer pain points and improve service delivery
- Train and empower employees to provide exceptional customer experiences
- Continuously monitor and analyze performance metrics to drive improvement
- Create a culture of service excellence and customer loyalty
SPC and TQM are essential tools for organizations seeking to improve quality, reduce costs, and enhance customer satisfaction. By integrating SPC and TQM, organizations can create a comprehensive and sustainable quality management system that drives continuous improvement and ensures long-term success.
Long Tail Keywords for Alt Attribute
- Statistical Process Control (SPC) in manufacturing and services
- Total Quality Management (TQM) in manufacturing and services
- Benefits of SPC and TQM for quality control and continuous improvement
- Implementing SPC and TQM in manufacturing and service industries
- Role of SPC and TQM in enhancing customer satisfaction and loyalty
- Best practices for integrating SPC and TQM for optimal results
5 out of 5
Language | : | English |
File size | : | 5561 KB |
Text-to-Speech | : | Enabled |
Screen Reader | : | Supported |
Enhanced typesetting | : | Enabled |
Word Wise | : | Enabled |
Print length | : | 154 pages |
Do you want to contribute by writing guest posts on this blog?
Please contact us and send us a resume of previous articles that you have written.
Book
Novel
Chapter
Text
Story
Genre
Magazine
Paragraph
Shelf
Foreword
Synopsis
Annotation
Footnote
Tome
Library card
Autobiography
Memoir
Reference
Encyclopedia
Narrator
Character
Resolution
Librarian
Catalog
Borrowing
Periodicals
Study
Scholarly
Reserve
Academic
Journals
Rare Books
Special Collections
Interlibrary
Literacy
Study Group
Storytelling
Reading List
Theory
Textbooks
Ethan Rutherford
Wallace O Chariton
William L Sharp
Peter Rosch
Amy Quick Parrish
Armin Nassehi
Jean Philippe Marre
William P Fox
Anna Nguyen
Stacy Thompson
Vasileios Yfantis
Kathleen Duey
Chikako Ozawa De Silva
Kathleen M Fallon
Michail Sygar
Peter Brandvold
David A Bogart
Heather Gardam
Hayley Dartnell
Seth Godin
Light bulbAdvertise smarter! Our strategic ad space ensures maximum exposure. Reserve your spot today!
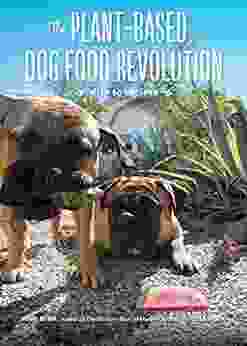

- Marvin HayesFollow ·15.4k
- Liam WardFollow ·11.5k
- Davion PowellFollow ·14.9k
- Carter HayesFollow ·14.7k
- Wade CoxFollow ·2.8k
- José MartíFollow ·2.4k
- Trevor BellFollow ·9k
- Sean TurnerFollow ·16.3k
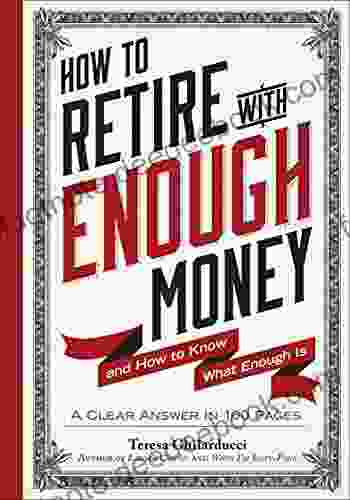

Unveiling the True Meaning of Enough: A Comprehensive...
: In the relentless pursuit of progress and...
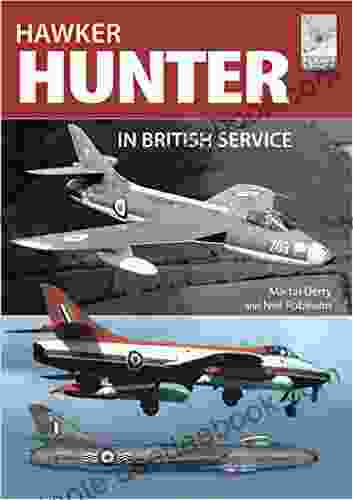

Hawker Hunter: The Jet Fighter that Shaped British...
Nestled in the halls of aviation...
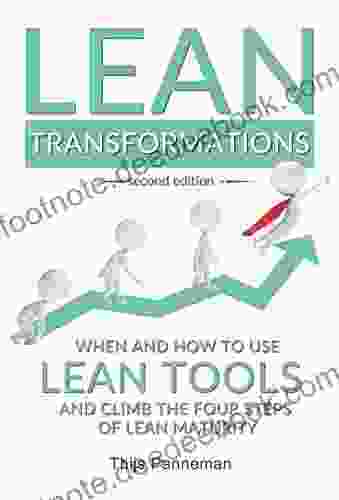

When and How to Use Lean Tools and Climb the Four Steps...
Lean is a management...
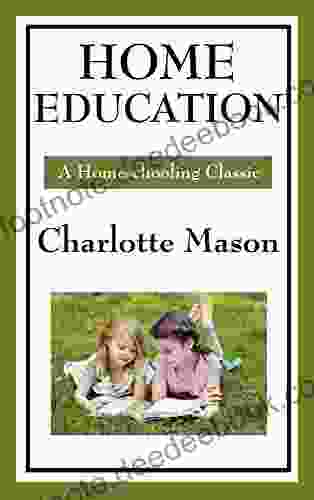

Volume of Charlotte Mason Original Homeschooling: A...
Charlotte Mason's original...
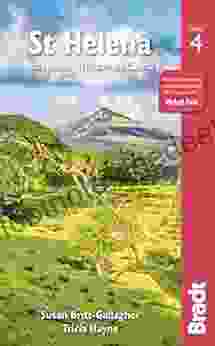

Ascending Tristan da Cunha: A Comprehensive Guide to...
Prepare yourself for an extraordinary journey...
5 out of 5
Language | : | English |
File size | : | 5561 KB |
Text-to-Speech | : | Enabled |
Screen Reader | : | Supported |
Enhanced typesetting | : | Enabled |
Word Wise | : | Enabled |
Print length | : | 154 pages |